Our Streamlined Process
Our process is designed to ensure efficiency and quality. We focus on delivering exceptional results by combining innovative techniques with proven methods.
%20(1).avif)
Detailed Insight into Our Process
Our process is meticulously designed to merge efficiency with quality. By incorporating state-of-the-art techniques alongside tried-and-true methods, we deliver granite of exceptional durability, finish, and consistency—ready to meet a wide range of project needs.
.avif)
Step 1
Extraction
At Afrika National Granite, the extraction process begins with a detailed geological analysis to identify and select granite of the highest quality. This careful selection ensures that only the most structurally sound and visually appealing stone is chosen for processing.
Once a site is prepared, our team uses precision drilling and advanced wire sawing techniques to extract the granite in clean, controlled blocks. These methods not only reduce waste but also help preserve the natural strength, texture, and integrity of the stone.
This approach allows us to maintain consistency across projects while respecting the natural environment from which the stone is sourced.
Step 2
Quality Inspection
At Afrika National Granite, quality assurance is a critical part of our production process. Every granite block undergoes a multi-stage inspection to ensure it meets our high standards before moving forward. This includes checking for structural integrity, evaluating colour consistency, and examining surface texture for uniformity.
Our team also inspects each block for any cracks, blemishes, or natural imperfections that could affect performance or appearance. By taking the time to carefully evaluate each piece, we ensure that only the finest granite—free from flaws and visually consistent—is selected for further processing.
.avif)
.avif)
Step 3
Cutting
The cutting stage is where precision truly matters. We utilize advanced cutting machinery, including high-performance Italian multi-wire saws and gangsaw multiblade cutting plants, to ensure that each granite piece is cut with the utmost accuracy.
These state-of-the-art tools allow us to slice raw granite blocks into slabs of varying thicknesses, ranging from 20mm to 200mm, with exacting precision. Throughout the process, careful monitoring ensures consistency in size, shape, and quality, preserving the integrity of each slab.
This advanced equipment enables us to deliver a flawless finish while also enhancing efficiency and cost-effectiveness in comparison to older machinery.
Step 4
Finishing
In the finishing stage, each granite slab undergoes a meticulous process to achieve the desired surface texture and appearance. Using advanced Italian technology, slabs are polished to a brilliant shine, or brushed and honed to meet specific design requirements.
For unique textures, we employ a specialized flaming plant to create distinctive finishes such as flaming or antiquing, which add character and depth to the stone, highlighting its natural variations.
Once the finishing treatments are applied, each slab is rigorously inspected to ensure it meets our stringent quality standards, ensuring a result that meets any of the specifications requested. This careful attention guarantees that every slab is ready for use in a wide variety of projects.
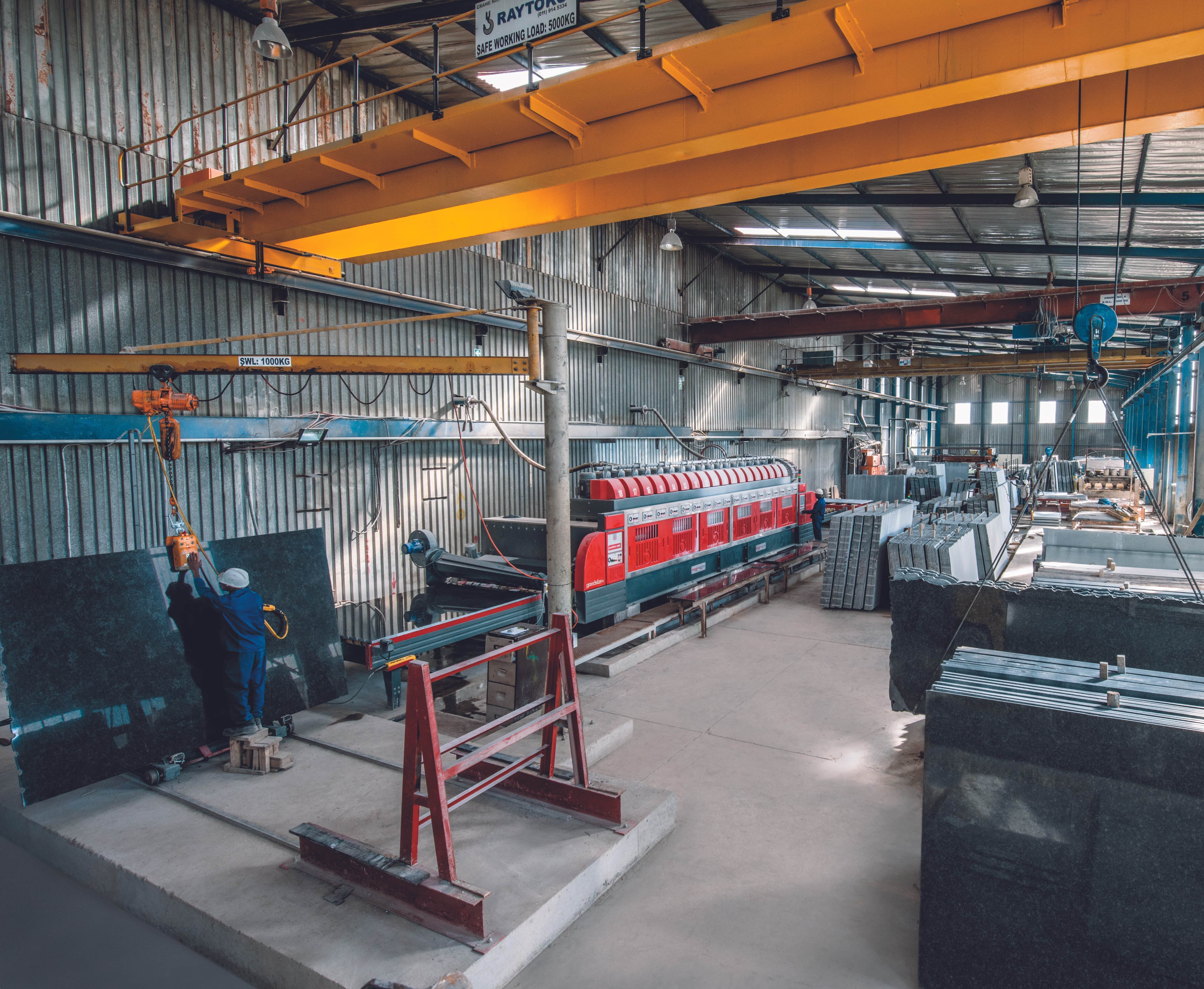
%20(1).jpg)
Step 5
Cut-to-Size
In the cut-to-size phase, precision is critical. By employing advanced state-of-the-art technology, each granite piece is carefully tailored to exact dimensions, ensuring a high level of uniformity and consistent quality throughout.
Our process utilizes bridge saws to cut granite slabs according to detailed specifications, accommodating diverse project requirements. This method not only supports large-scale developments but also meets the needs of specialized installations, ensuring that every piece is accurately produced to maintain both structural integrity and aesthetic consistency.
Step 6
Prepared
After a comprehensive quality inspection, the granite products undergo a meticulous preparation process for transit. Each piece is carefully wrapped and secured using specialized protective materials designed to cushion against impacts and environmental stressors.
Multiple layers of insulation and reinforcement are applied to safeguard the stone's surfaces and edges, reducing the risk of damage during transportation. This thorough preparation ensures that the granite maintains its integrity from the workshop to the final destination, meeting the demands of various logistical scenarios without compromising quality.
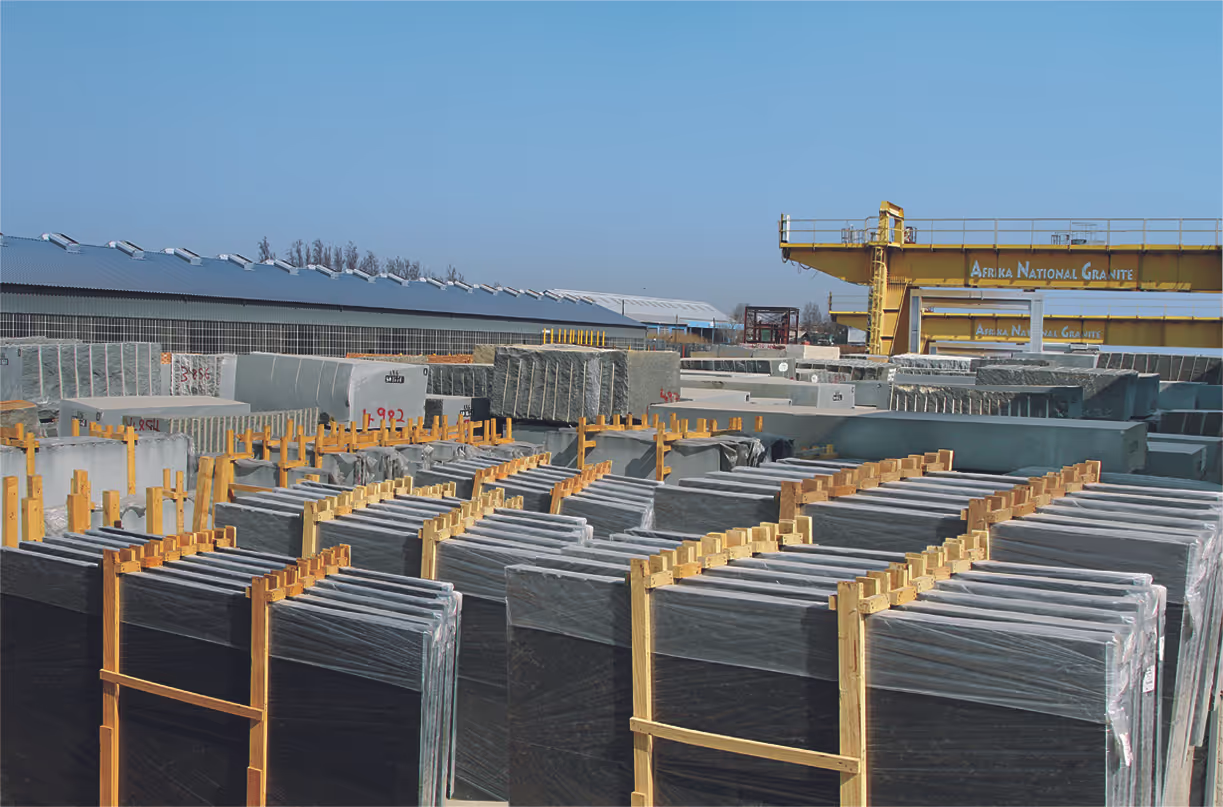
.avif)
Step 7
Packaged
Following the preparation phase, the granite products are carefully loaded into secure shipping containers. Each piece is meticulously positioned and stabilized using a combination of customized restraints and separation materials to prevent any movement or shifting during transit.
This careful packaging process is designed to absorb impacts and minimize vibrations, ensuring that the granite remains intact and free from damage while in transit.
These enhanced measures work together to maintain the granite’s structural integrity and pristine appearance, ensuring that the products are delivered safely and without damage to their final destination.
Step 8
Delivered
The granite products are set for delivery—whether for local distribution or international export. During transit, specialized handling procedures and equipment ensure that each container remains stable and is continuously monitored to guard against any external vibrations or unforeseen impacts.
Rigorous loading protocols and transport checks are in place to maintain the integrity of the containers, ensuring that the products remain undisturbed throughout their journey.
This comprehensive and carefully managed process guarantees that each product reaches its final destination intact, preserving both its quality and meeting scheduled delivery times.
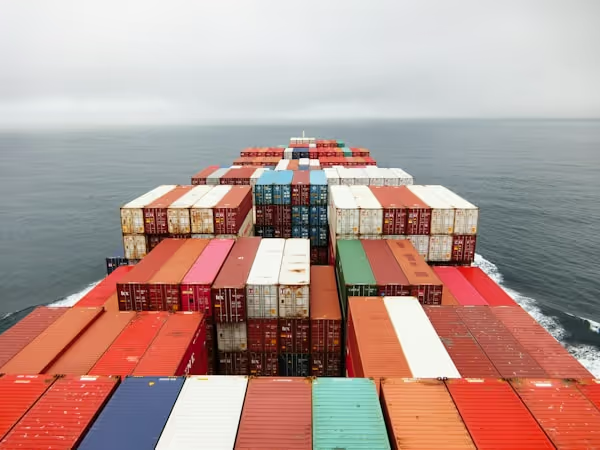
A granite partner you can trust
We are committed to providing exceptional granite solutions with integrity and reliability. Our team ensures that every product is handled with the utmost professionalism and attention to detail.
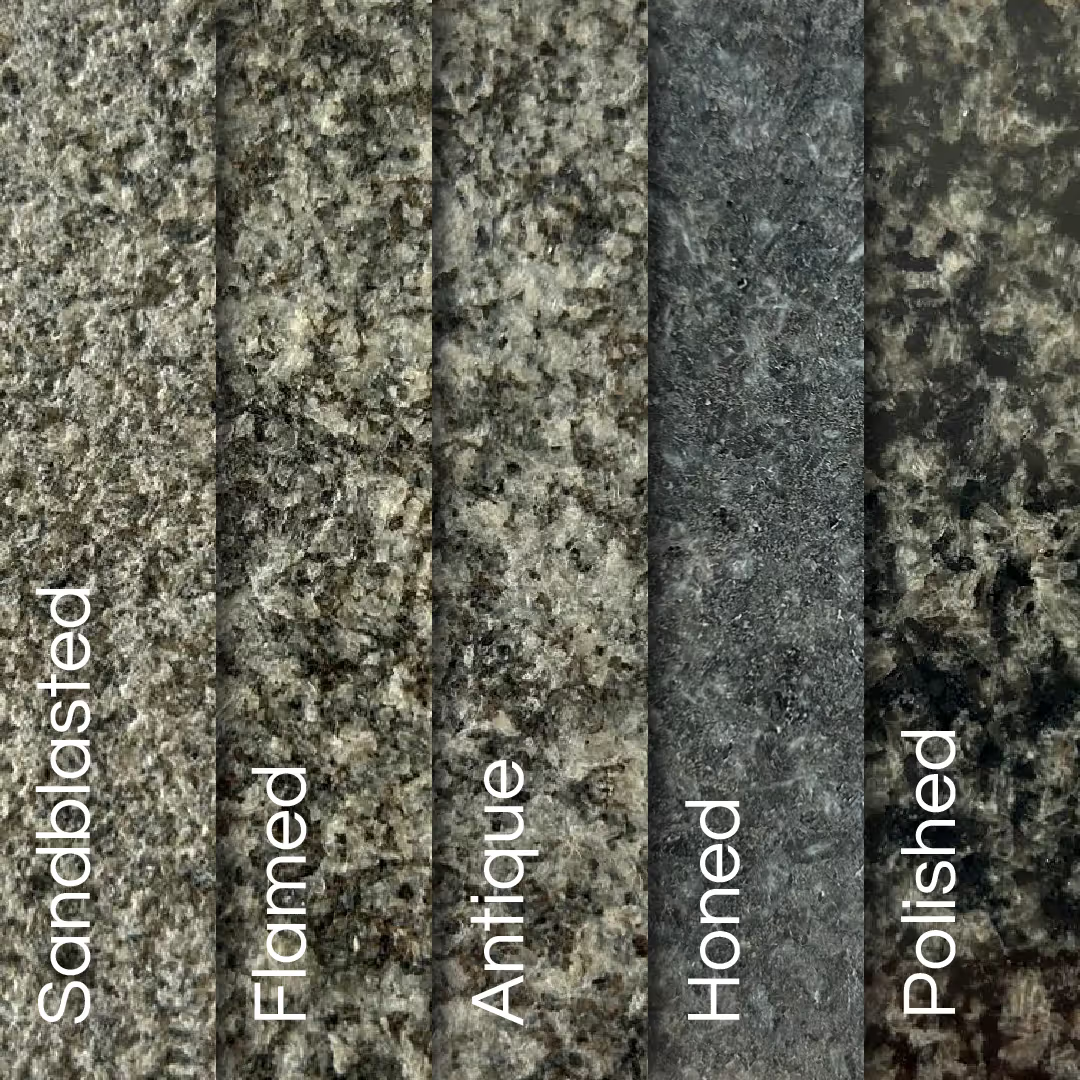
High-quality granite supplied with care and consistency
We take pride in providing premium granite, ensuring every piece meets our high standards through consistent quality control and care.
Long-standing history in the granite industry
With decades of experience, we have established a strong reputation in the granite industry, consistently supplying exceptional products worldwide.
Quarry ownership equals better quality control
Owning our quarries allows us to maintain strict quality control, ensuring every piece of granite meets our high standards. This direct oversight enables us to consistently deliver top-quality products and materials.
The latest in cutting and polishing technology
We use state-of-the-art cutting and polishing technology to ensure precision in every piece of granite we produce. This advanced equipment allows us to deliver a flawless finish while also being more efficient and cost-effective.
Multi-national, with exports to 25 countries
Our granite is exported to 25 countries, showcasing our commitment to quality and global reach. This wide distribution reflects the demand for our products in various markets around the world.
Explore the ANG Stone Collection
Our range of granite materials combines skilled finishing with consistent quality—offering durable, versatile surfaces for everything from custom fabrication to large-scale builds.
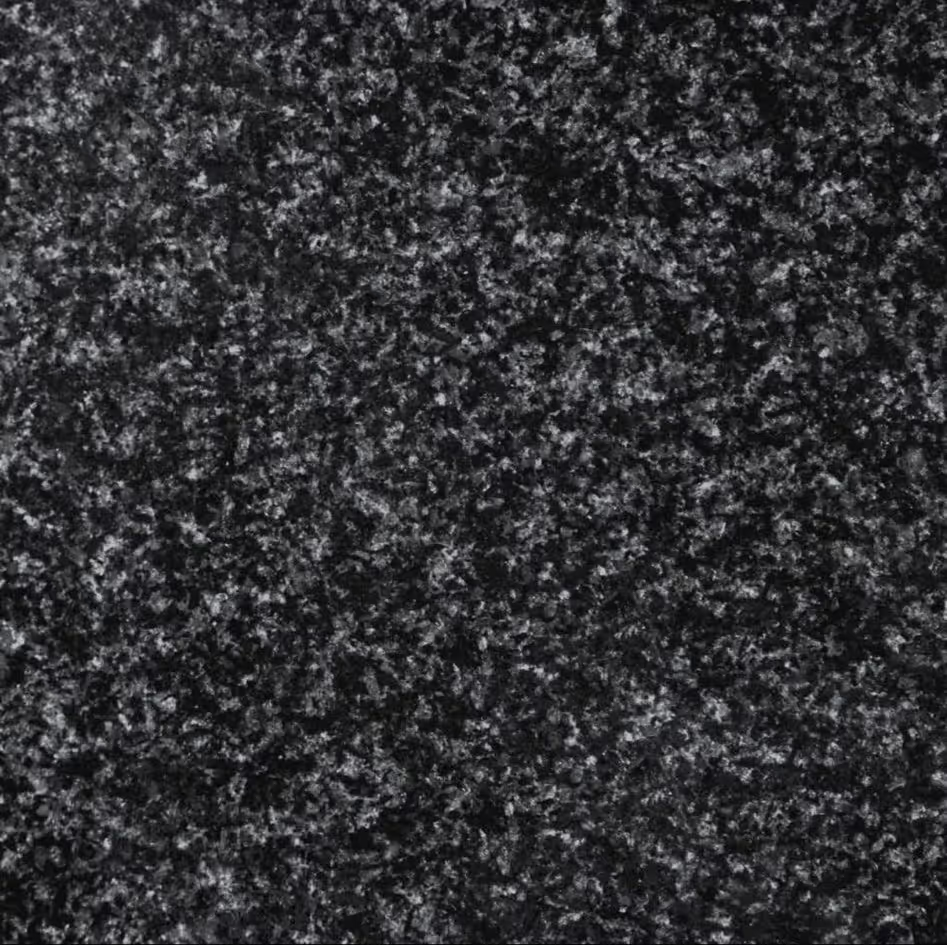
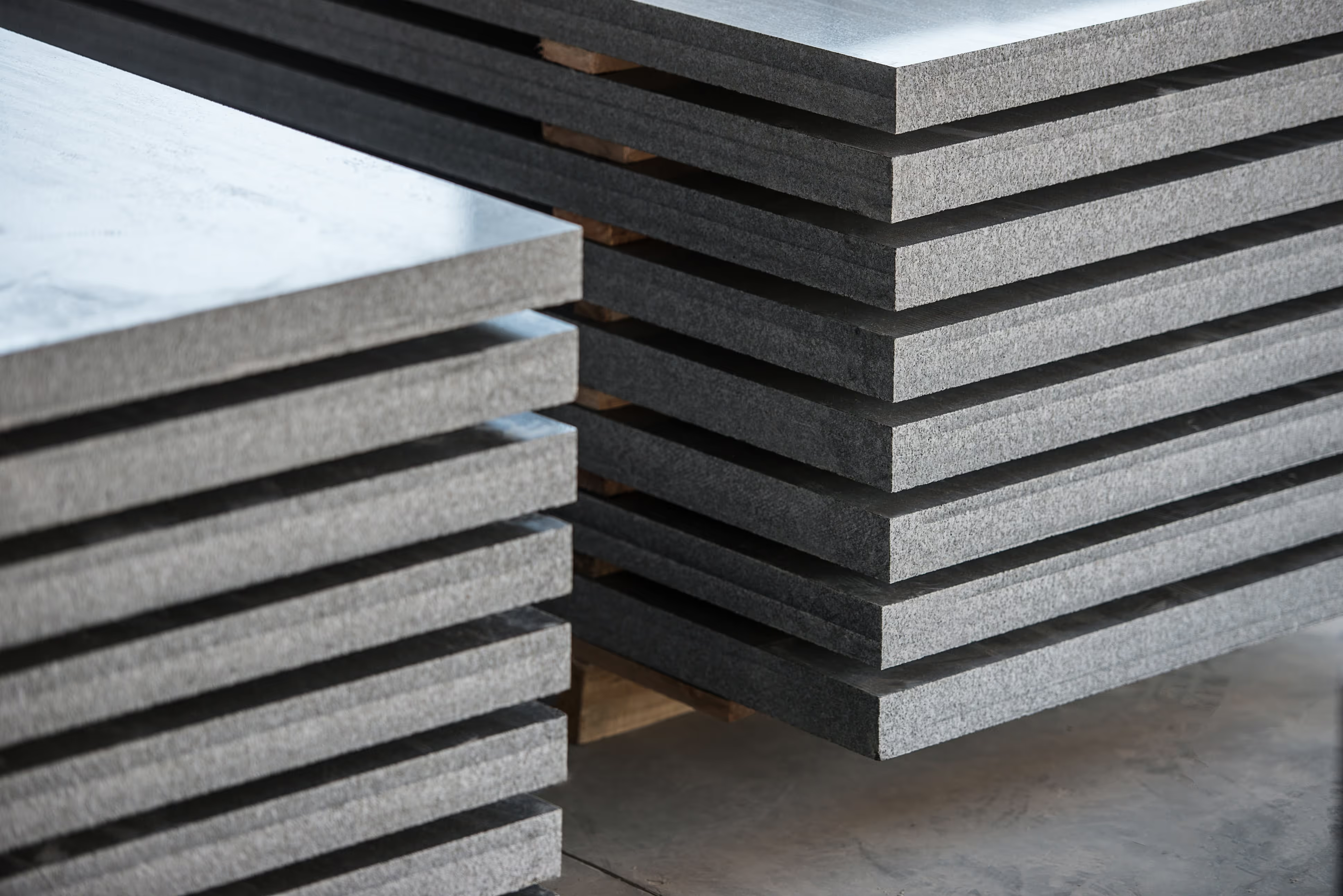